Camsı metaller herhangi bir kristal yapıya yani düzenli bir atomik örgüye sahip olmayan amorf malzemelerdir. Ancak bu malzemeler elektriksel ve mekanik özellikleri ile ilgi çekicidirler. Bu sahip oldukları özellikler arasında manyetik özellikleri ile ürün koruma/güvenlik sistemlerinde (electronic article surveillance), hızlıca soğuyan yapısı ile biyouyumlu biyomalzeme olarak kullanılması gibi geniş uygulama alanlarına sahiptirler.Camsı metaller hakkında KBT Bilim Sitesi’nde “Metalik Camların Özellikleri ve Tarihçesi” başlıklı bir yazı yayınlamıştık ve bu yazının devamı olarak camsı metallerin üretim yöntemlerini ele alacağız.
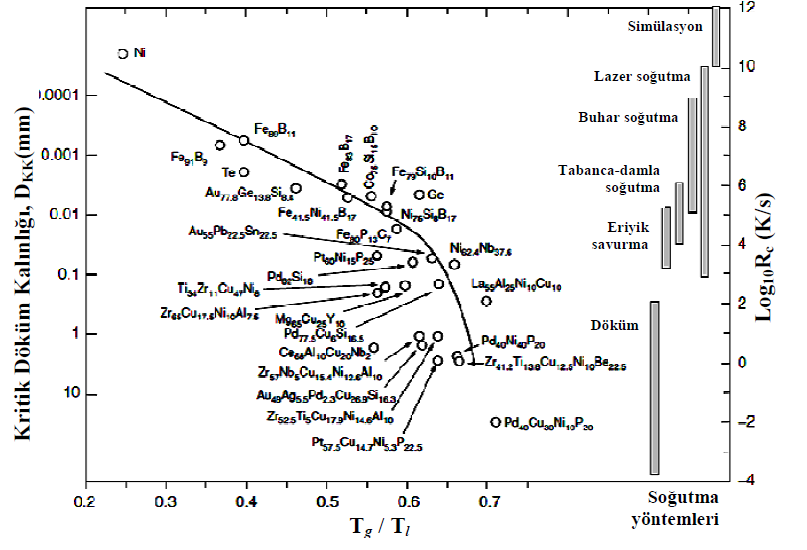
Şekil 1: Çeşitli Alaşımların Kritik Soğutma Hızı, İndirgenmiş Cam Geçiş Sıcaklığı ve Soğutma Yöntemlerinin Karşılaştırılması [1]
1. Damlacık Soğutma ve Piston Örs Yöntemi
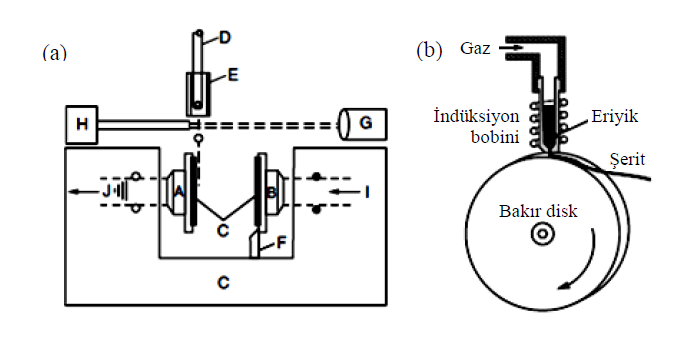
Şekil 2: (a) Damlacık Soğutma ve (b) Piston Örs Yöntemi [1]
Damlacık soğutma ve piston örs yöntemlerinde 1-4 cm çapında, 50 mikron kalınlığında disk numuneler elde edilebilmektedir. Bu yöntemle küçük kütleli bir alaşım numunesi indüksiyon bobini arasında yüksek frekanslı akım kullanılarak askıda ergitilir. Elektrik akımı kesildiği anda eriyik damlacığı düşer ve sensörlü pinömatik ve elektromanyetik olarak hareket ettirilen iki düz piston arasında çok hızlı bir şekilde ezilerek soğutulur [1].
2. Vakumla Emme ve ya Enjeksiyonla Döküm
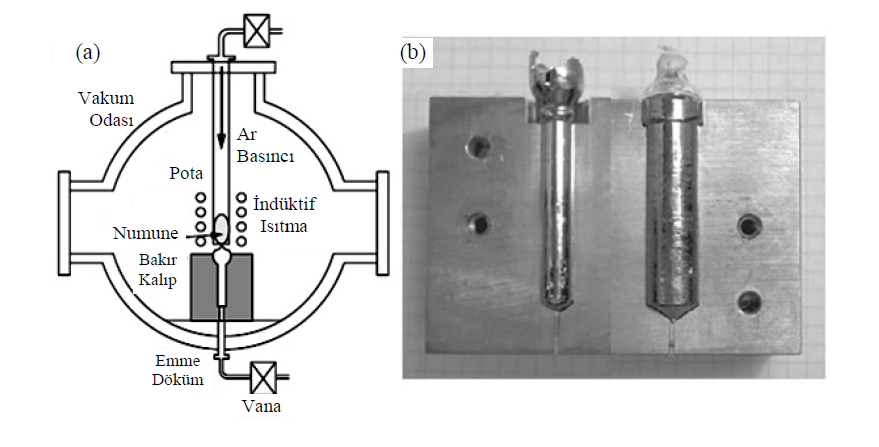
Şekil 3: (a) İndüksiyon ile Isıtılan ve Bakır Kalıpta Şekillendirme İşleminin Yapıldığı Döküm Haznesinin Şematik Gösterimi. (b) Malzemenin Bakır Kalıp İçerisindeki Görüntüsü [1]
Bu yöntem düzeneğin vakum çemberi içinde olduğu ve oksitlenmenin minimum olacağı şekilde olması için tasarlanmıştır. Burada sınırlayıcı faktörlerden birisi yüksek ergime sıcaklığına sahip alaşımların ergitilmesinin zorlaşmasıdır. Bunun için indüksiyon yerine ark kullanılmaktadır.
Sistemdeki Ar gazı basıncı 0,3 – 1 bar civarındadır ve bu itici güç sayesinde vakumun da etkisiyle sıvı eriyik bakır kalıba beslenir [1].
3. Üfleme (Şişirme) Yöntemi
Yumuşama sıcaklığının üstüne ısıtıldığında insan nefesiyle bir camın şekillendirilebildiği yaklaşık 2000 yıl önce keşfedilmiştir. Yaklaşık 40 yıl önce de polimer malzemelerin bu yöntemle üretilebileceği keşfedilmiş ve bu yöntem plastikler için teknik bir üretim yöntemi halini almıştır.
Elde edilebilir bir geometriye sahip camsı alaşımların üretimi günümüzde genellikle eni boyu sınırlı hızlı soğutma sistemlerine sahip kalıplara dökümle sağlanmaktadır. Yüksek en/boy oranına sahip ince kesitlerin üretimi teknoloji açısından önemlidir. Sadece çok hassas dengeye sahip süreç parametreleri bu yöntemi ticari olarak bazı geometriler için cazip kılmaktadır.
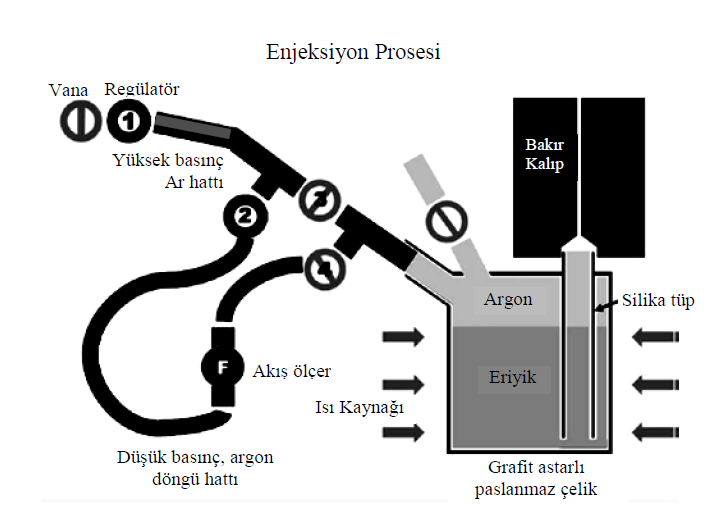
Şekil 4: Camsı Metallerin Üretiminde Kullanılan Düşük Basınçlı Döküm Düzeneğinin Şematik Gösterimi [2]
Camsı metallerin aşırı soğutulmuş sıvı bölgesinde plastik olarak şekillendirilmesi, süperplastik şekillendirme, termoplastik şekillendirme ve sıcak şekillendirme gibi çeşitli terminolojilerle tanınmaktadır. Bu süreç net şekillerin üretimi, mikro ve nano replikasyon, ekstrüzyon, amorf köpüklerin sentezi, levha halinde süper plastik şekillendirme gibi çeşitli uygulamalarda kullanılmaktadır. Şekil 5’de Schroers ve arkadaşları tarafından camsı metaller için hazırlanmış üfleme işlemi ile kalıplama düzeneği gösterilmektedir. 60-80 mm çapa sahip yaklaşık 1 mm kalınlığındaki disk şekilli numuneler başlangıç malzemesi olarak kullanılmaktadır. Bu işlemde termoplastik özelliği yüksek olan Zr44Ti11Cu10Ni10Be5 alaşımı kullanılmıştır. Üfleme tekniği için, tüm düzenek rezistans kullanılarak ısıtılmakta ve disk numunenin alt ve üst kısımlarında meydana getirilen basınç farkı ile camsı metal şekillendirilmektedir. Bu işlem, disk şekilli numunenin üst kısmından basınç uygulanması ve ya kalıp boşluğundaki basıncın azaltılması ile yapılabilir. Şekillendirme işlemi, camsı metalin kalıp boşluğuna dokunması veya basınç farkının tahliyesi sonuçlandırılır.
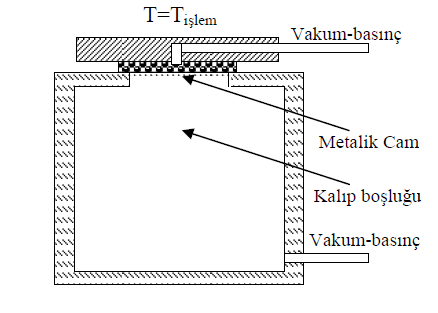
Şekil 5: Üfleme Yönteminin Şematik Görünümü [3]
3.1 Levitasyon Ergitme ve Döküm
Literatürde, belirli bir konteyner kullanılarak yapılan ergitme işlemlerinde heterojen çekirdeklenme meydana gelme ihtimalinden bahsedilmektedir. Bundan dolayı, birçok araştırmacı gerekli kritik soğuma hızını ve kristallenme kinetiklerini incelemek üzere herhangi bir ergitme kabı kullanılmadan gerçekleştirilen teknikler araştırmışlardır. Bununla ilgili olarak Kim, Busch ve Johnson aşırı soğutulmuş sıvının kritik soğuma hızını ve kristallenme kinetiklerini daha kalitatif incelemek için elektrostatik levitasyon prosesi uygulamışlardır [4]. Bu işlem de diğerleri gibi ultra yüksek vakum şartları altında yapılmaktadır. Numunenin ısıtılması ve ergitilmesi kuvars ampul veya lazer ısıtma kaynağı ile yapılmaktadır. Numune sıcaklığı numuneye temasın olmadığı bir pirometre sayesinde ölçülmektedir. Daha sonra eriyik haldeki damla bakır kalıp içerisine yerçekimi etkisiyle düşmektedir. Bu yöntemde de ergitilen malzemenin ağırlığı sınırlıdır [4].
3.2 Arc Melting Yöntemi
Camsı yapıyı oluşturacak metal tozları bakır tablaya konur ve tabla cihaza yerleştirilir. Ortam vakum altına alınır ve Argon (Ar) ile süpürülür. Süpürme yapıldıktan sonra toz karışım ark ile ergitilir ve bu işlem karışım çeşidine göre tekrarlanır. Ergiyik bakır altlıktan su geçirilerek hızlı soğutulur.
Bu yazımızda camsı metal üretim yöntemlerini birkaç başlık altında böylece ele almış olduk.
Kaynaklar:
1. Groza J.R., Shackelford J.F., Lavernia E. J., Powers M.T., 2007, “Materials Processing Handbook”, CRC Press, Taylor&Francis Group, FL, USA
2. Laws K.J., Gun B., Ferry M., 2006,“Effect of Die Casting Parameters on Production of High Quality Bulk Metallic Glass Samples”, Mater. Sci. and Eng., A 425, pp114-120
3. Schroers J., Pham Q., Peker A., Paton N., Curtis R.V., 2007, “Blow Molding of Bulk Metallic Glass”, Scripta Materialia, 57, 341-344
4. Busch R., Kim Y.J., Johnson W.L., 1995, “Thermodynamics and kinetics of the undercooled liquid and the glass transition of the Zr41.2Ti13.8Cu12.5Ni10Be22.5 alloy”, J. Appl. Phys., Vol.77, No.8, 4039-4043